Garment Manufacturing Program
Unlock your clothing production potential with Ready-to-wear garment production management program (IGS), a complete intelligent solution Increase efficiency, accuracy, and efficiency throughout the production process It can improve the production process and optimize management efficiency at every step of the garment production process. In addition, the program allows for accurate and rapid labor cost calculations. Using barcode or RFID technology that is connected to a central database. This allows managers to provide in-depth analysis for each job. and effectively reduces production costs as well
IGS understands the challenges of producing ready-made garments. Our programs are designed to manage a wide range of data across all departments. From product details Customer requirements, sourcing, coordination, production, inventory, shipping and export documentation help ensure your information is up to date. Easy to access and accurate
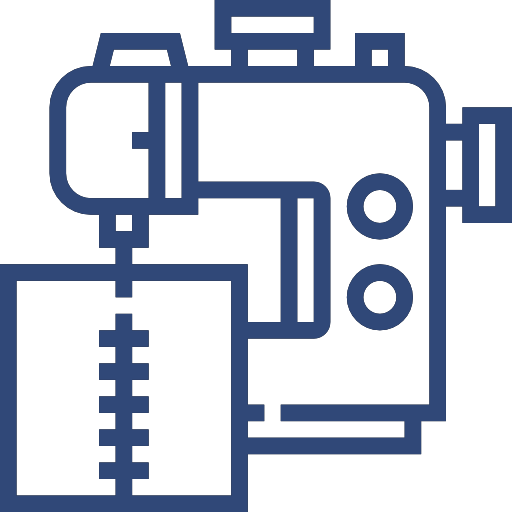
Can manage orders
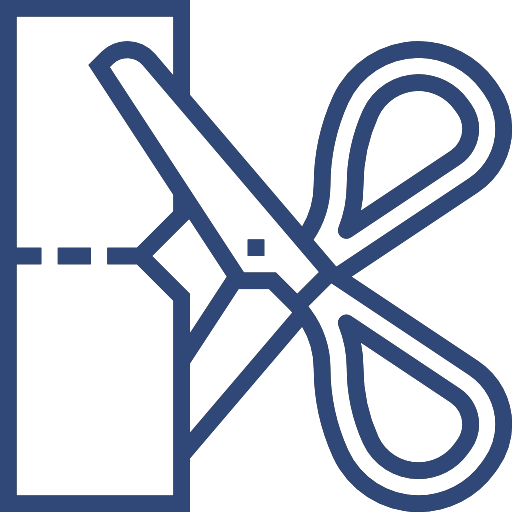
Helps control raw materials for sewing
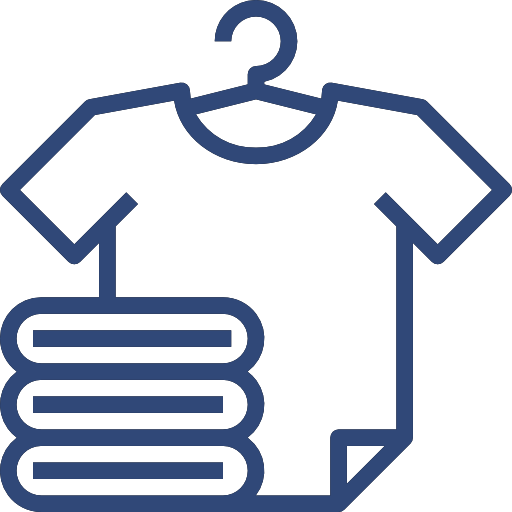
Tags are the function of clothing production.
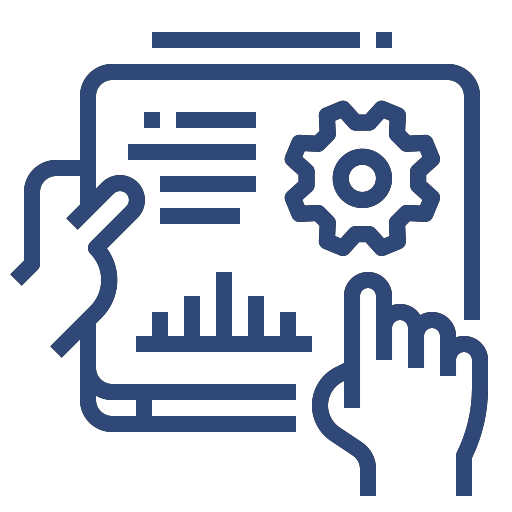
Can sort orders by importance
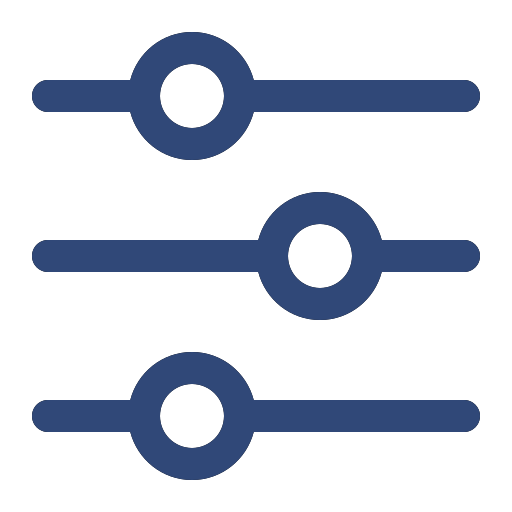
Can control production
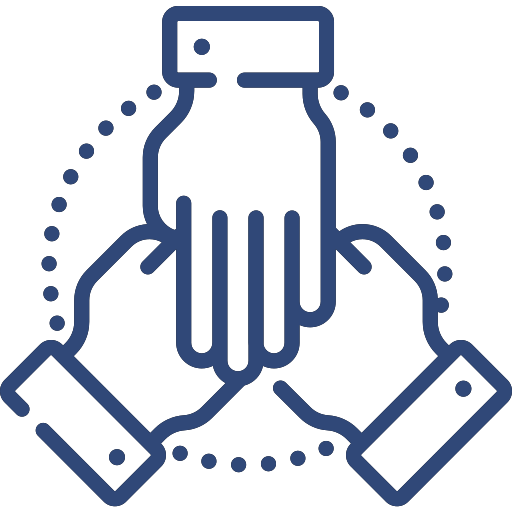
Support work in many departments
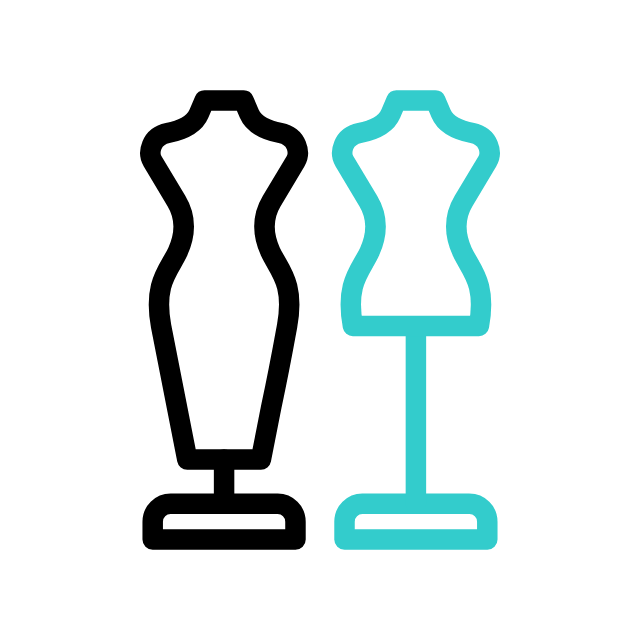
Highlights of the program
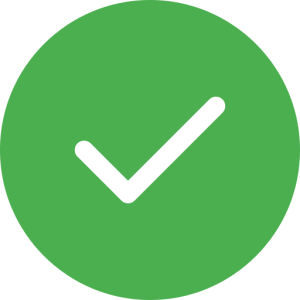
Support teamwork by separating work hours.
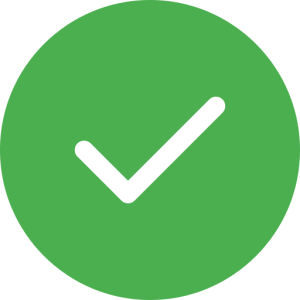
Open production orders, check production status quickly
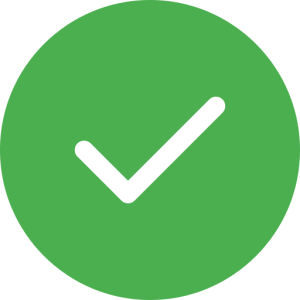
Control the receipt and distribution of raw materials to clearly see production costs.
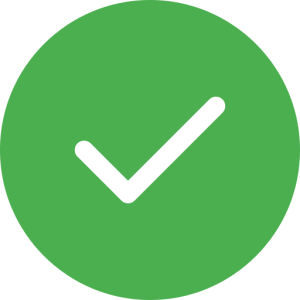
The SAM Report system can issue delivery notes, invoices, and various bills.
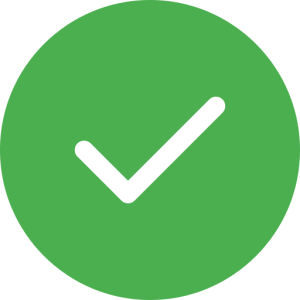
Use a barcode system to calculate labor costs and control production.
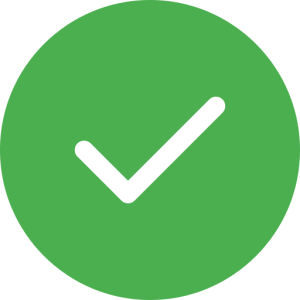
Open production order, product details, material list, sewing and delivery date.
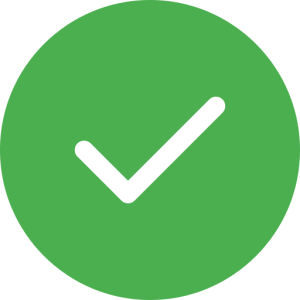
Copy and edit old production orders For easy repeat work
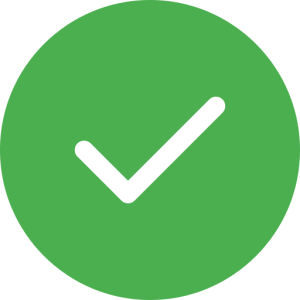
Production order approval system change control maintain correctness
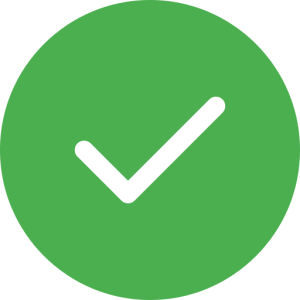
Link purchasing systems, purchase orders, import raw materials and notify about out of stock products
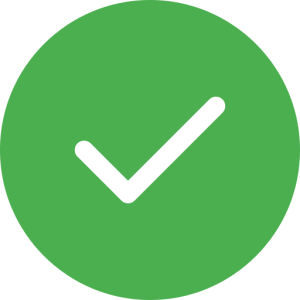
Print a coupon tag from the system to identify which bundle belongs to which production order and which part.
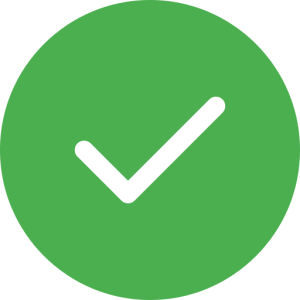
Our system supports effective teamwork.
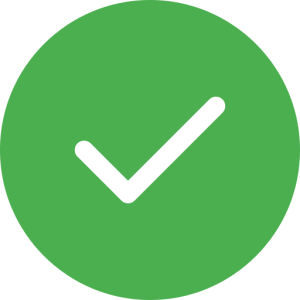
Calculate labor costs per piece of work by scanning a barcode.
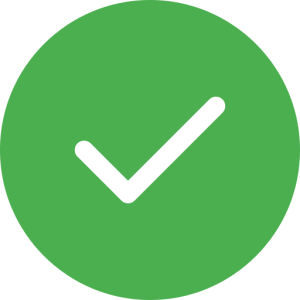
Print employee wage statements for each employee.
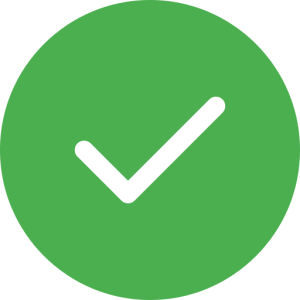
The system can work with the time recording system.
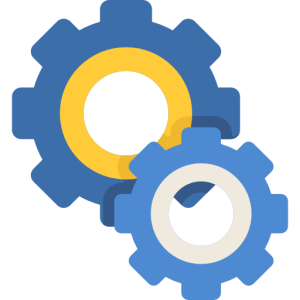
Setting material details
- The system specifies 3 types of material details: cutting, sewing, and decorating.
- Materials can be identified in 2 ways: code name/selected name. You can add stores and contact numbers.
- Automatic material code generation system You can set your own name, link your account’s BOM.
- You can name the material yourself. Convenient copying and editing Add details of type, color, size, unit.
- The system links customer names with materials. Separate materials into waste Easy to find and use
- Information management system for suppliers, contacts, products, minimum orders Notification when products are almost out of stock
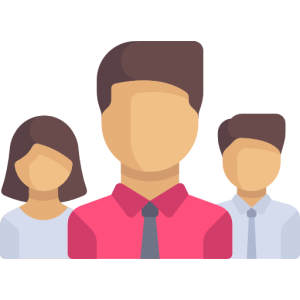
User configuration
- Users can configure work processes and labor costs for each step.
- Use generic templates or customize them for clients/jobs. Save them in the system. Use them anytime.
- You can name the running process as you want.
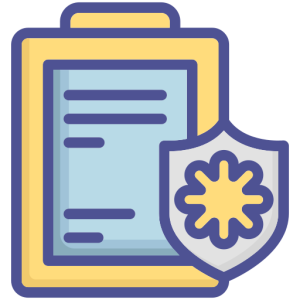
Order configuration
- Fabric purchase order creation system (main raw materials) and accessories Retrieve supplier information Find items quickly print purchase order
- Reference the production order number and customer name. Used to manage incoming stock
- Easily find and view orders. Filter by month, year, supplier, number. Access orders by reference number. Search for code and item name Filter related items
- Each purchase order line can include multiple comments on a single purchase order. The name and approval of the person opening each purchase order is required. and can be configured to include or exclude VAT for each order.
- Inventory notification system in advance for a specified number of days/times. Supports discounts. Print purchase orders (PDF/A4) and send to suppliers. and automatically generate PO numbers
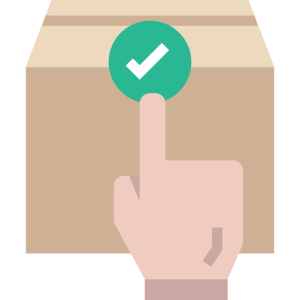
Receive the product
- You can reference information on a purchase order by simply searching for the purchase order number. All information will be displayed to receive the order without having to re-enter the information. It is possible to receive some items and leave others for future pickup for each order. In the event that all products are received You can mark shipments as complete to avoid confusion with purchase orders.
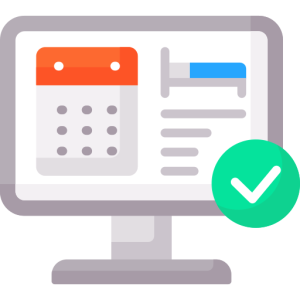
Product reservation
- You can reserve products in stock before they go on sale.
- Receiving and issuing goods.
- Picking up and issuing products is designed to be user-friendly and only the correct items can be selected.
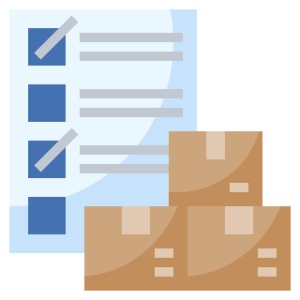
Order production
- The production order is the main document. Collect production data for each batch. Mix with the amount from the cutting table.
- Fabric cutting table made to order. Record work details Easily print summary and cutting details.
- The system supports entering cutting details in 3 formats: Details by size ratio (S-M-L-XL for example), Details by format. or multiplying the number of fabric layers of each lot to get the total number of cuts.
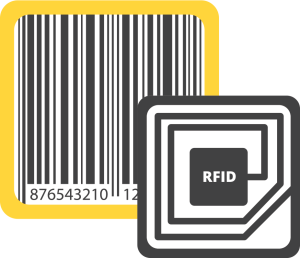
Barcode or RFID system
- Barcodes are part of the system. Numerical data comes from production order numbers, sizes, sides, colors, and piece rates, as well as cutting data from the cutting table. This makes each set of numbers unique and impossible to repeat.
- This coupon or RFID tag is given to the employee responsible for each job. To specify the wages that employees will receive upon completion of work.
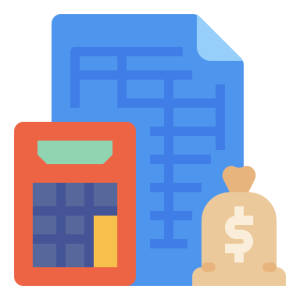
Employee wages
- Easy to use program for receiving barcode or RFID data. By selecting the employee name or employee code Then scan the barcode or receive RFID information when the employee creates it. Then the program will automatically display the amount received. According to the piece rate, multiply the number of pieces in the bundle. And individual coupons or RFID tags cannot be reused.
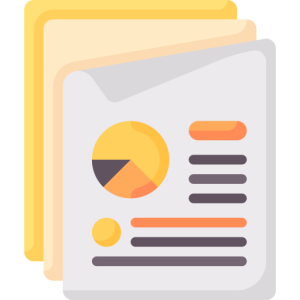
Production cost summary report
- The Production Cost Summary report shows the actual production costs for each production order. Summary of all direct labor and equipment (direct materials) used in production
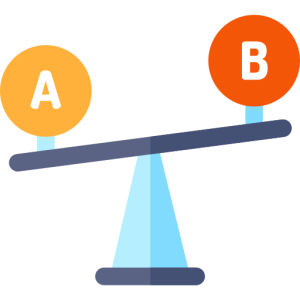
Balancing production lines
- Another important part of the program is line balancing, which is covered by the SAM report. In this report, basic information on the number of operators per production line can be entered. The amount of work time (in minutes) and factory costs (in minutes) are compared to the number of pieces produced. This helps achieve optimum productivity by ensuring the production line is balanced and work is divided equally between operators.